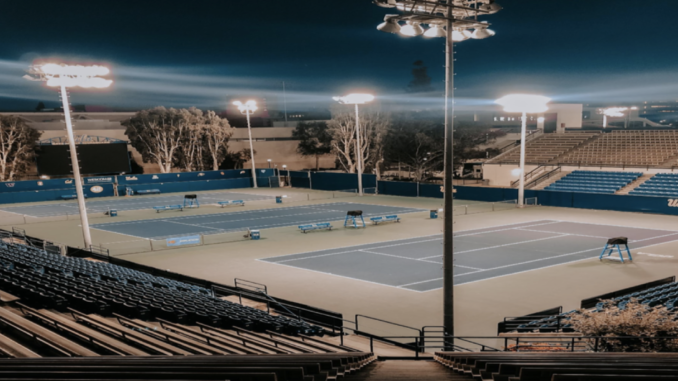
When it comes to electrical projects, terminal blocks ensure safe and reliable connections. These small yet essential components are used to securely connect electrical wires, making them a cornerstone of electrical engineering in everything from home wiring to complex industrial systems.
Innovations in terminal block design, such as advanced materials and compact configurations, have made it easier to optimize installations for performance and safety. However, choosing the right terminal block is more than just a technical and safety decision – it impacts compliance and overall project success. We explore the considerations so you can make the best choice for your project.
Understanding project requirements
The first step in selecting the right block or terminal block strips is understanding the specific needs of your project. Each application has unique requirements for current and voltage ratings, which dictate the type of terminal block you should use.
The current rating refers to the maximum current the terminal block can handle without overheating or failing. For example, in residential applications, typical current ratings may range between 10 and 30 amps, while industrial setups may require significantly higher ratings. Consulting your project’s electrical specifications is critical to ensuring compatibility and safety.
Voltage ratings are equally important. Terminal blocks are often designed for specific voltage levels, whether extra low-voltage applications under 50 volts or high-voltage installations exceeding 600 volts. Failure to match your terminal block to the correct voltage rating can lead to insulation failure, short circuits, or even catastrophic electrical fires.
Another key consideration is the type of connection. Screw-type terminal blocks are widely used for their reliability and secure connections, but they can be time-consuming to install. Spring-cage and push-in connections offer quicker and more modern alternatives, making them increasingly popular in industrial and high-density wiring applications.
Material and construction
Terminal blocks are made from materials tailored to their intended use. Conductive parts are typically made from copper or brass, offering excellent conductivity and durability. The housing is usually made from high-performance plastics that resist heat and electrical arcing. Projects exposed to harsh conditions, such as high humidity or corrosive chemicals, should prioritize corrosion-resistant materials and finishes.
Environmental factors also play a role. Terminal blocks are often rated for specific temperature ranges and moisture resistance, indicated by IP ratings. For example, an IP67-rated terminal block offers protection against dust and water, making it ideal for outdoor or industrial environments.
Safety and compliance
Compliance with safety standards is non-negotiable. In the US, look for terminal blocks certified by organizations such as UL (Underwriters Laboratories) or meeting IEC (International Electrotechnical Commission) standards. These certifications ensure the product has been rigorously tested for safety and performance. Features like insulation, grounding options, and finger-safe designs further enhance the safety of your electrical system.
Physical characteristics
Space constraints often dictate the size and type of terminal block. Compact designs are ideal for high-density wiring projects, but they may sacrifice ease of access for maintenance. Mounting options also matter. DIN rail-mounted terminal blocks are versatile and popular in industrial settings, while panel-mounted terminal blocks offer added stability.
Ease of installation is another critical factor. Clear labeling and color-coded terminals simplify wiring and reduce the chance of errors, while tool-less options like push-in connections save time.
Leave a Reply